Production cost planning using Qlik Sense Enterprise and K4 Analytics
- Production
- Poland
- Qlik Sense Enterprise (on-premise) and K4 Analytics
- 9 months

Overview
The client is a large manufacturing company with complex production and business processes. A pressing need in the organization was a necessity to update forecasting data and automate the processes of creating plans and reports, which used Excel files.
The implementation of the tools was aimed at partial automation of work, maintaining data consistency and speeding up the process of planning rates, mark-ups and recording current production costs. The implementation of the tool allowed a significant acceleration in the process of generating reports and determining planned values, by creating the following Business Intelligence applications:
- Analytical application for tracking production costs;
- Planning application for verification, determination and planning of fixed and variable rates;
- Planning application for verification, determination and planning of percentage mark-ups on material.
Context
An important step in determining production costs is calculating the actual machinery and labor rates. A separate issue is determining the percentage mark-ups added to the costs resulting from the processing of materials, taking into account, among other things, the cost of electricity and other utilities.
In the case of multi-stage production, which involves many teams or departments, e.g., the welding department, paint team, assembly department, and many more – in the reality of high volatility in component prices – it is very difficult to estimate the approximate cost of production of a given product, even after it is manufactured.
In order to increase the capabilities and at the same time reduce the load on the ERP system, we made the decision to transfer additional calculations to Qlik Sense, which significantly improved the efficiency of the process and reduced the time required to obtain a meaningful result.
In addition, the project used an extension to Business Intelligence tools called K4 Analytics. The solution allowed BI applications to embed data editing formats, which was crucial in reflecting the process of determining and planning rates and other cost elements.
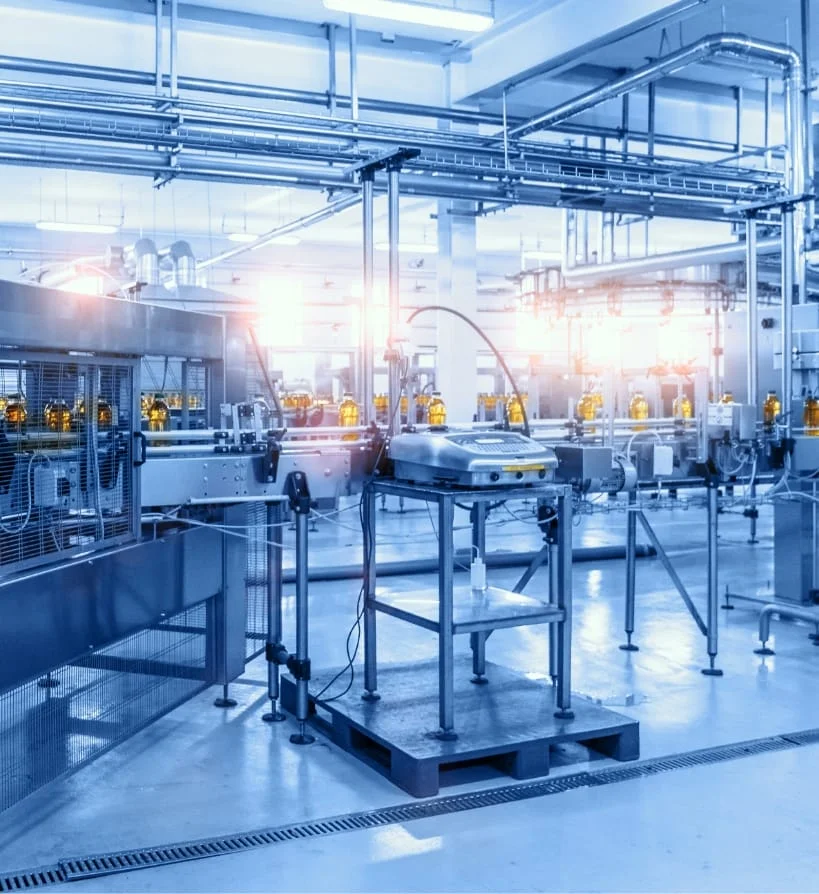
Challenge/Problem
Until now, the process of cost analysis and planning rates and surcharges was done manually, which was extremely time-consuming and required a lot of work by representatives of the Controlling department. Cost analysis was carried out in Excel files, in which the client manually supplemented last month’s data, correcting some values based on experience and knowledge, assigning them to the appropriate resource groups. Once the sheets were completed, labor and machine rates were determined using formulas, which also required manual data entry and correction, such as employee availability.
Due to the necessity of entering values manually, the process was exposed to a significant risk of error, and the data was not available immediately after the month was closed. In order to obtain a summary of monthly costs, it was necessary to enter the essential information into multiple separate files and manually determine the missing data. Historical costs related to human resources and machine usage were not stored (i.e., versioned). This data was scattered in Excel files (so-called flat files) on the user’s disk, and therefore, it was not publicly available, which could have a significant impact on the overall operation of the company.
The process of determining rates and other cost elements was based on the experience of the Controlling department representative, which made it impossible to reproduce the report in IT solutions, using only parameters downloaded from the system. The implementation required the participation of an experienced controller, and therefore, the success of the existing process depended on the availability of a specific employee.
In summary, the existing process was burdened with the following problems:
- Time-consuming – activities performed manually, requiring a considerable amount of work by a qualified controller;
- Lack of access to current data – inability to analyze production costs in real time;
- Lack of historical data – no versioning of costs related to the work of production employees and the operation of machines;
- Lack of data consistency – manual correction of data caused final reports to differ from the data available in the ERP system.

Solution
Implemented tools allowed the significant acceleration of the process of generating reports and determining planned values by creating the following Business Intelligence applications:
- Analytical application for tracking production costs;
- Planning application for verification, determining, and planning fixed and variable rates;
- Planning application for verification, determining, and planning percentage markups for materials.
The implementation of the BI tool – Qlik Sense – allowed for addressing the client’s problems and implementing an effective system for analyzing and forecasting production costs.
The automation of processes allowed for significant reduction of time in work execution and improved data consistency, by eliminating intermediate reports, created in Excel files so far. Currently, data is downloaded directly from the ERP system and modified using the K4 Analytics tool. In addition, by implementing a personalized system for versioning rates and markups, the problem of lack of access to historical data has been solved, allowing monitoring and comparing data for selected periods.
Benefits
- Automation of the process allowed to reduce time-consuming activities by 25%
- Significantly streamlined the work of the Controlling department, by reducing the amount of work required to generate a set of analytical reports
- Reducing risks arising from potential human error and unavailability of a qualified employee
- Ensure data consistency by directly connecting the source (ERP system) with the BI tool - Qlik Sense
- Ability to track over time and version dynamic changes in costs
- Creation of automatically refreshed analytical reports for verification of costs in all available dimensions, e.g. in relation to departments involved in a given process, a specific production order or product group
- Increasing the accuracy of production cost determination, resulting in more accurate planning of the company's operations
- Introducing precise data access management by assigning permissions at the level of roles and user types

What have we learned
Working with such a large production company was a very interesting challenge for us. Despite implementing only the Controlling department, the work showed us how interconnected the individual controlling processes and other departments of the company are.
The implementation allowed us to increase our knowledge of:
- The various ways of determining key production parameters;
- Detailed ways of determining costs and their actual recording, determining, and tracking;
- Controlling processes and procedures in compliance with Polish and European laws, as well as how to automate them effectively;
- Creative use of available technologies.
The implementation of planning applications has allowed us to understand the problems faced by large, international production companies and how we can solve the indicated problems.
Qlik and K4 systems, by automating data entry and verification processes, significantly affect the development and operation of the organization where they are implemented. Implementing the tools even in one department can have a fundamental impact on the workflow of the entire enterprise. The example of a large, international production company shows how to streamline the flow of current cost information throughout the organization in a relatively easy manner.
Here you will find expert support on Qlik + K4
See other case studies
Replication of MRP Areas between SAP MDG and SAP ECC
Implementation of the ERP system enova365 in many companies of the Opolgraf brand
Implementation of the company’s acquisition process by merging and integrating systems
Report optimization in the FMCG industry
Discover our capabilities
19+ years of experience
Since 2006 we have been helping our clients implement and develop systems and applications that streamline business processes. Owing to our know-how, our Partners are able to fully utilize the technologies of the future.
1000+ completed projects
We approach each project individually. We employ technologies that improve the enterprise functioning and management. The joint implementation of each projects brings our clients closer to perfection in managing a modern organization.
450+ employees
We have an appropriate team of experiences and qualified experts in many fields. Consultants, analysts, programmers and PMs. We have been successfully implementing even the most complex projects that streamline the development of organizations around the world.
50+ countries where we have carried out deployments
Based on our unique skills, we implement innovative projects around the world. We conquer new markets and constantly enter new areas. A comprehensive approach allows us to ensure the development of companies from numerous industries and sectors.
Contact us!
Let’s talk! Are you interested in our solutions? Our experts are happy to answer all of your questions.